Lee Hsun Lecture Series
Topic: Development of high performance wrought magnesium alloys containing only common metals by conventional hot extrusion
Speaker: Prof. Shigeharu Kamado
Department of Mechanical Engineering, Nagaoka University of Technology
Director of Research Center for Advanced Magnesium Technology,
Nagaoka University of Technology, Japan
CV-Prof. Shigeharu Kamado
1. Introduction
Recently, from the view point of improvement of fuel consumption, Mg alloys with the lowest specific gravity among metallic materials are paid much attention as structural materials for transportation vehicles such as automotives, airplane, high speed trains etc. However, applications of extruded Mg alloys to structural components are still limited due to the fact that strengths and heat resistance of conventional Mg alloys such as AZ31 alloy (Mg-3wt%Al-1wt%Zn-0.3wt%Mn alloy) are generally insufficient in comparison with those of steels and Al alloys, leading to achieve unsatisfactory weigh reduction. Additions of rare earth elements (RE) like Gd, Y etc. have been well known to result in remarkable age hardening, extraordinary high strengths possible to be compared with those of Super Duralmin and high hat resistance up to 250℃ by precipitation of metastable β' phase (1)-(5), but RE containing magnesium alloys are very expensive. Therefore, industrial companies strongly demand development of high performance magnesium alloys composed of only common metals which are able to obtain easily everywhere and are also cheap. In the very recent past, Jayaraj reported that Mg-Zn-Ca (6) and Mg-Al-Ca (7) alloys large age hardening by precipitation of monolayer ordered GP zone parallel to basal plane, which are similar to the ordered GP zone observed in Mg-Zn-RE alloys (8). Furthermore, the ordered GP zones in grains are also found to improve notably heat resistance (9),(10). Based on the results, we aim to improve strengths and heat resistance of wrought magnesium alloys by additions Ca and Mn to Mg-Al based alloys, and therefore, systematically investigated the relationship between nano- and micro-structural changes during extrusion and heat treatment and obtained mechanical properties. In this lecture we explain (1) the microstructural changes including dynamic recrystallization behavior and dynamic precipitation during hot extrusion, (2) precipitates contributing to age hardening and (3) relationship between nano- and micro-microstructures such as bimodal microstructure, recrystallized grain size, texture, precipitaes etc. and mechanical properties.
2. Development of high strength and heat resistant Mg-Al-Ca-Mn alloy containing high amount of alloying elements by extrusion(11),(12)

We fabricated extruded cylindrical bars with a diameter of 13.4 mm using a direct chill (DC) cast Mg–Al–Ca–Mn billet with a nominal composition of Mg–3.6Al–3.3Ca–0.4Mn (wt.%) (denoted as AXM4304) with a diameter of 60 mm, which contains fine eutectic microstructure consisting of a-Mg and Al–Ca intermetallic compound (C14 and C36 phases). The extrusion was carried out at 350℃ using a direct extrusion method under a low ram speed of 0.1 mm/ s and an extrusion ratio of 20. The extruded bar shows a bimodal grain structure and consisting of fine equiaxed dynamically recrystallized (DRXed) grains of about 1mm and elongated strips of unrecrystallized (unDRXed) areas (white area in Fig. 1(b)). The fine lamellar Al–Ca compounds observed in the DC cast billet are fragmented into fine particles of about 0.5 mm and are dispersed along the grain boundaries (Fig. 1(a)). The fine fragmented Al–Ca compounds suppress the grain growth during the hot extrusion process, resulting in the refinement of DRXed grains. The basal planes in the coarse unDRXed area are strongly aligned along the extrusion direction, but those in the fine DRXed grains have relatively random orientation. As a result, the former areas have a relatively low Schmid factor for the basal slip, while the latter grains have a relatively high Schmid factor for the basal slip. On the other hand, nanoscale plate-like precipitates lying on the basal planes and also fine spherical ones are formed at the unDRXed areas even when extruded at a high temperature of 350℃ (Fig.2 (a)). From the three-dimensional atom map, the plate-like precipitates are found to be enriched with Al and Ca, and are considered to be the Al2Ca phase, while the spherical ones consist of Al and Mn with a small amount of Ca. Such plate-like precipitates are also observed even in the as-cast sample (Fig. 2(b)). They precipitate during cooling after solidification. However, the plate-like precipitates in the as-extruded sample are longer and thicker than those in the as-cast sample. The growth of the plate-like precipitates and the formation of the spherical ones suggest that dynamic precipitation occur during the hot extrusion at 350℃. The results suggest that such nanoscale precipitates are thermally stable even at high temperature of 350℃. Furthermore, we confirmed that they can also precipitate when extruded at higher temperature of 400℃(12). By such microstructural changes the as-extruded sample shows a high tensile 0.2% proof stress (TPS) of 410 MPa, a high ultimate tensile strength of 420 MPa and a moderate elongation to failure of 5.6%. The compressive 0.2% proof stress (CPS) is 350MPa, so the yield asymmetry defined by CPS/TPS is 0.83. Also rotational bending fatigue strengths at room temperature and 150℃ are 240MPa and 160MPa, respectively (12). The strengths of the as-extruded AXM4304 sample are much higher than those of the as-extruded AZ31 sample. Furthermore, the mechanical properties of the as-extruded AXM4304 sample are in fact superior to those of the T6-treated heat-resistant 4032 aluminum alloy sample (Al–Si–Cu–Mg–Ni alloy). These high strengths are attributed to the combined effects of (1) fine dynamically recrystallized grains pinned with fragmented Al–Ca intermetallic compounds, (2) a strong basal texture of unrecrystallized area, and (3) fine nanoscale plate-like Al2Ca precipitates and spherical Al8Mn5 precipitates.
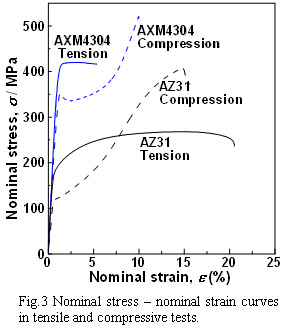
3. Development of high speed extrudable magnesium alloy having age hardenability
We have succeeded in strengthening by an application of low speed extrusion of 0.12m/min to Mg–3.6Al–3.3Ca–0.4Mn (wt.%) alloy (11). However, such low speed extrusion leads to low productivity and also high production cost. Therefore, industrial companies strongly desire development of Mg alloys having high speed extrudability corresponding to that for Al window sash. Thus we investigate possibility to apply high speed extrusion to Mg-Al-Ca-Mnalloys containing dilute alloying elements. We could carry out high speed extrusion of 48 m/min by using a dilute Mg-0.27Al-0.13Ca-0.21Mn (wt.%) alloy homogenized at 500C for 24 hours. The extrusion speed is maximum in our laboratory and is comparable to that for 6063 Al window sash. When low extrusion speed is applied bimodal microstructures consisted of dynamic recrystallized (DRXed) grains and unDRXed areas are formed. But when the extrusion speed is higher than 12m/min homogeneous DRXed microstructures could be obtained in whole area, and basal texture is weakened. With an increase in extrusion speed DRXed grain size increases due to an increase in heat generation during the extrusion, but the grain size is refined when extrusion speed is 48m/min. In the extruded sample ordered GP zones also precipitate by T5 treatment after the extrusion, resulting in age hardening (Fig.4). In T5-treated samples tensile strength and proof stress decrease with an increase in extrusion speed, but elongation increases. Nominal stress – nominal strain curve in tension test of T5-treated sample (Fig.5). Tensile strengths and proof stresses of T5-treated sample are 220MPa and 260MPa respectively, and are far superior to those of T5-treated 6063 Al alloy. Also the values are comparable to those of T6-treated 6061 and T5-treated 6N01Al alloys, which are practically applied to a body panel of automotives and a double skin outer panel of Shinkansen, respectively, by an application of only T5 treatment after extrusion.
References
(1) I.A. Anyanwu, S. Kamado and Y. Kojima: Mater. Trans., 42 (2001), 1206-1211.
(2) I.A. Anyanwu, S. Kamado and Y. Kojima: Mater. Trans., 42 (2001), 1212-1218.
(3) T. Honma, T. Ohkubo, K. Hono, and S. Kamado: Mater. Sci. Eng. A, 395 (2005), 301-306.
(4) T. Honma, T. Ohkubo, S. Kamado, andK. Hono: Acta Mater., 55 (2007), 4137-4150.
(5) T. Homma, N. Kunito, S. Kamado: Scripta Mater., 61 (2009), 644-647.
(6) K. Oh-ishi, R. Watanabe, C.L. Mendis and K. Hono: Mater. Sci. Eng. A, 526 (2009), 177-184.
(7) J. Jayaraji, C.L. Mendis, T. Ohkubo, K. Oh-ishi and K. Hono.: Scripta Mater., 63 (2010) 831-834.
(8) D.H. Ping, K. Hono, J.F. Nie: Scripta Mater., 48 (2003), 1017–1022.
(9) T. Homma, S. Nakawaki, S. Kamado: Scripta Mater., 63 (2010), 1173-1176.
(10) T. Homma, S. Nakawaki, K. Oh-ishi, K. Hono, S. Kamado: Acta Mater., 59 (2011), 7662-7672.
(11) S.W. Xu, K. Oh-ishi, S. Kamado, F. Uchida, T. Homma, K. Hono: Scripta Mater., 65 (2011), 269-272.
(12) S.W. Xu, K. Oh-ishi, S. Kamado, H. Takahashi, T. Homma: Mater. Sci. Eng. A, 542 (2012), 71-78.
